Electromagnetic Stirring (EMS) has emerged as a transformative technology with versatile applications, revolutionizing diverse industries. From the heart of steel production to the intricacies of metallurgical processes, EMS has proven its worth by optimizing manufacturing efficiency and elevating operational outcomes.
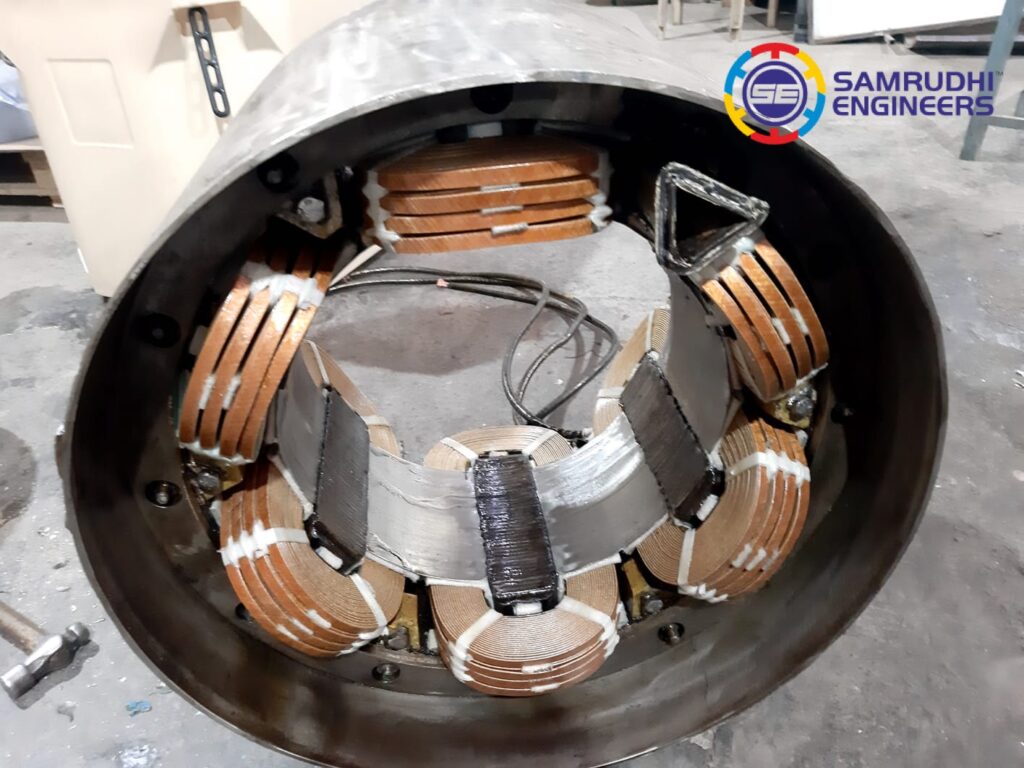
Enhancing Steel Production:
In the realm of steel manufacturing, EMS takes center stage, dynamically agitating molten steel in casting blanks. This process optimizes the transfer of molten steel and heat exchange, leading to improved surface cleanliness, reduced porosity, and enhanced machine throughput. EMS is reshaping the landscape of steel production, contributing to efficiency gains and heightened productivity.
The EMS Advantage:
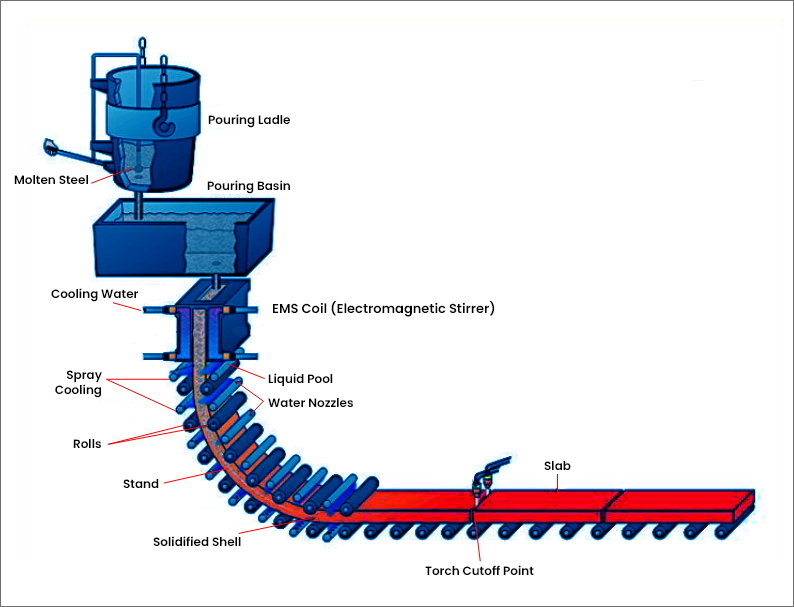
EMS systems utilize electromagnetic fields to induce stirring in molten metals. This results in more effective mixing and homogenization of the molten material. This is crucial in metallurgical processes to ensure uniform composition and properties of the final product.
The stirring action induced by EMS helps in distributing heat more evenly throughout the molten material. This can prevent localized hotspots and ensure consistent temperature profiles, contributing to improved product quality and reduced defects.
Electromagnetic stirrers are generally more energy-efficient compared to traditional mechanical stirrers. They don’t require direct contact with the molten material, reducing wear and tear on equipment and minimizing maintenance costs.
The controlled stirring provided by EMS can help minimize the adhesion of molten metal to crucible walls, reducing the amount of metal loss during the manufacturing process. This is particularly important in processes where materials are expensive or scarce.
Since EMS systems operate without direct physical contact with the molten material, there is a reduced risk of contamination and operator exposure to hazardous substances. This contributes to a safer working environment.
How EMS helps mitigate impurities:
- Enhanced Mixing: EMS involves the application of electromagnetic fields to induce stirring in the molten steel. This stirring action facilitates better mixing of the metal, helping to disperse and homogenize alloying elements. As a result, impurities and inclusions are more evenly distributed throughout the molten steel.
- Reduced Segregation: One of the challenges in steel casting is the uneven distribution of alloying elements, leading to segregation. EMS helps minimize this issue by promoting uniform mixing, thereby reducing the likelihood of localized concentrations of impurities. This contributes to a more consistent composition in the final cast product.
- Minimization of Inclusions: The stirring action induced by EMS helps break up non-metallic inclusions and particles present in the molten steel. This contributes to the overall cleanliness of the steel, reducing the presence of undesirable impurities and improving the material properties.
- Improved Cleanliness: EMS assists in achieving a cleaner molten steel by reducing the presence of impurities such as oxides and non-metallic particles. This improvement in cleanliness positively impacts the surface quality and overall integrity of the cast steel.
In conclusion, EMS, championed by Samrudhi Engineers, stands at the forefront of technological innovation, weaving its magic across various industries. From refining steel production to shaping the quality of cast products, EMS is a game-changer, unlocking new possibilities and pushing the boundaries of manufacturing excellence. Explore the transformative impact of Electromagnetic Stirring (EMS) as a catalyst for innovation across industries with the expertise of Samrudhi Engineers.