The molten liquid during the continuous casting’s mould is churned through the use of the electromagnetic field, which helps generate defect-free and homogenous billets. During the investigation, the 2D computational model is effective for the stimulation of the electromagnetic stirring via the MHD, or magnetohydrodynamic module, in the ANSYS-FLUENT software. Electromagnetic stirring is used on a wide scale in the continuous casting process.
The billet’s solidified sheet is generated within the water-cooled vertical copper mold in the cooling’s primary phase. The primary stage of cooling gets investigated during the work without the employment of electromagnetic stirring.
In addition, the moving electromagnetic field of frequency 10Hz and intensity 0.1T is applicable in the vertical and horizontal directions for the electromagnetic stirring separately. As you go through this article, you can seek information about electromagnetic stirring in the continuous casting process:
What is EMS?
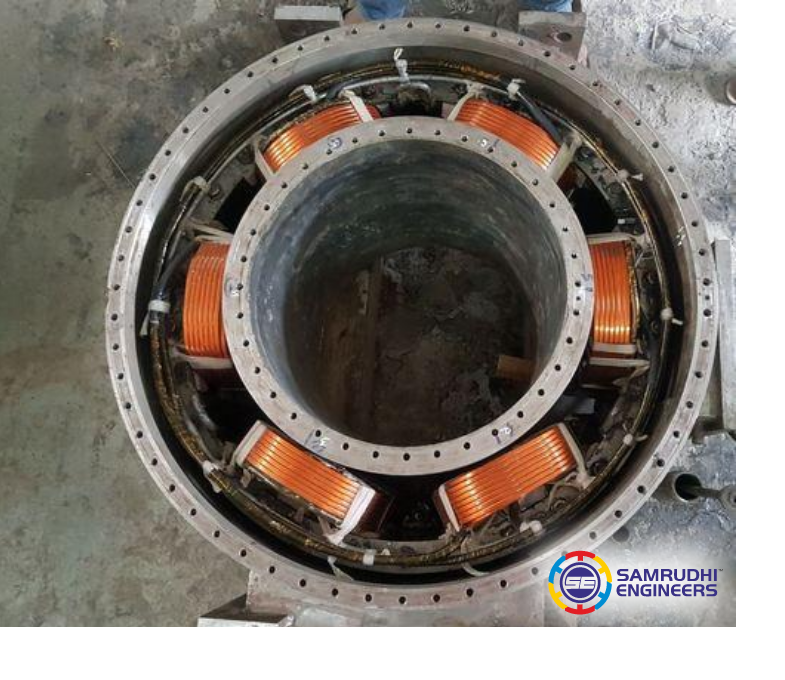
EMS contributes to being a powerful and direct process, which helps control the solidification process during the liquid steel’s continuous casting. The primary benefit of electromagnetic stirring is that it brings an improvement in the structural uniformity and quality at the cast product’s centre line.
The experimental results showcase beneficial results from the electromagnetic stirring on the steel’s microstructure. Through the EMS, it is possible to reduce the different kinds of defects within the strand. EMS affects the porosity and bubbles. The advantage of EMS is that it plays an integral role in boosting the continuous casting process’s productivity.
Types of EMS
The three different kinds of EMS include S-EMS, M-EMS, and F-EMS. M-EMS happens to be the process technology that is beneficial for the creation of tiny integrated devices, which is the combination of electrical and mechanical components. They are fabricated through the use of an integrated circuit, which helps in batching the processing techniques.
The F-EMS unit produces the electrical impulses, which are delivered through the electrodes present on the skin, closer to the muscles. The F-EMS aids in the recovery process. In addition, it enhances the work capacity more quickly than the past established techniques. The Strand electro-magnetic stirrer helps improve the slab’s internal quality, thereby increasing productivity.
EMS Application
The EMS Programs to the continuous casting process boasts a long history. It was used in the continuous casting machine once the continuous casting process began to generate steel industrially. The EMS systems in India in the continuous casting process impact the bubbles and inclusions.
The strand EMS opens the real EMS application doors to the continuous casting machine. The primary benefit of EMS is that it helps to acquire the higher equiaxed zone ratio for the centre of segregation suppression. The in-mould EMS systems are created to improve the cast steel’s surface quality with the agron bubbles and non-metallic inclusion entrapment suppression to the specific solidified shell.
EMS is boosting the productivity of the continuous casting process.
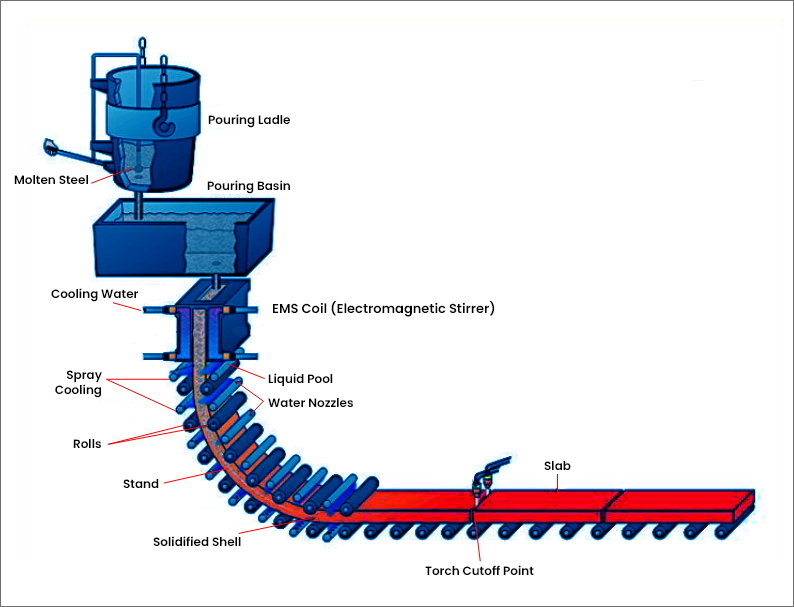
If you want to boost the continuous casting process’s productivity, the EMBR was created for the stabilization of the liquid steel flow during the continuous casting mould. Such a kind of EMBR is the creation of the local magnetic field, owing to which the DC magnet pair is installed in the SEN port’s neighborhood.
The imposed field will break the discharged flow from the specific SEN. In addition, the 2nd EMBR type happens to be the level magnetic field, which will uniform the magnetic field in the mould width direction. Another type of secondary EMBR happens to be the flow control mould. Today, there is a prerequisite development for the combination of EMBR and EMS electromagnetic stirring solutions.
The process ensures that the final product remains free from defects. Moreover, it plays an integral role in controlling the process. Electromagnetic devices bring an improvement in the process. The primary difference is that the stirrers will work under the AC current supply for the production of the dynamic magnetic fields.
The breakers are recognized to be permanent circuits and magnets which are fed by direct current and DC current. They play an integral role in generating consistent magnetic fields. The physical phenomena which occur within the mould happen to be the multi-physics problem, which is inclusive of the multiphase analysis, liquid flow, heat transfer, electromagnetic computation, and the solidification processes, in which every physics will rely on others.
Role of electromagnetic field
The continuous casting happens to be the pivotal process in the steelmaking process, as the liquid steel will shape into the billets and the blooms without rolling. Such a casting process will result in the steel pouring from the tundish. It is used for the collection of molten liquid within the vertical water-cooled copper mold.
The molten steel cooling within the mould happens to be the primary cooling zone, in which the solidified steel will be produced near the mould walls. This kind of solid shell boasts an adequate thickness at the mould exit, which helps to withstand the liquid metal ferrostatic pressure. The nonmetallic inclusion and the solute elements’ segregation impaired the strand quality. In addition, the liquid steel will be stirred for the production of heat transfer and the breakdown of the columnar dendritic solidification.
The stirring effect will be introduced using the external electromagnetic field within the mold. As the magnetic field is applied to the solid and liquid conduction, the eddy currents will be induced. It helps generate the electromagnetic force, which is referred to as the Lorentz force.
The liquid steel’s strong rotation within the mould is caused by Electromagnetic stirring (EMS), which ensures the sub-surface cleanness, thereby improving the surface quality. The mould stirring is used to change the flow pattern, thereby achieving the liquid character’s regeneration. In addition, it plays an integral role in generating the equiaxed grain structure.
The continuous casting’s stirring phenomenon improves the steel billets’ quality on the metallurgical effectiveness. The Electromagnetic Stirring helps improve the steel billet quality. A plethora of numerical and experimental investigations have been conducted for the exploration of the electromagnetic stirrer effect on steel continuous casting. It leads to an improvement in the strand quality.
Furthermore, Electromagnetic Stirring reduces defects at the subsurface and surface. Other than this, it enhances the solidification, thereby decreasing the breakouts at the mold exit. If you are looking for such services, Sumrudhi Engineering can be a great option to consider.